Naval Group skills up on multi-material WAAM thanks to Grade2XL
- aenserink
- Nov 2, 2021
- 3 min read
Demonstrate the potential of the process Wire Arc Additive Manufacturing and develop the necessary technologies are key challenges of the European project called Grade2XL for which Naval Group is a partner. This project has received funding from the European Union’s Horizon 2020 research and innovation program. The Grade2XL Design Contest is an activity enabling to disseminate WAAM. The first Grade2XL part, a node structure, had been produced at Naval Group.
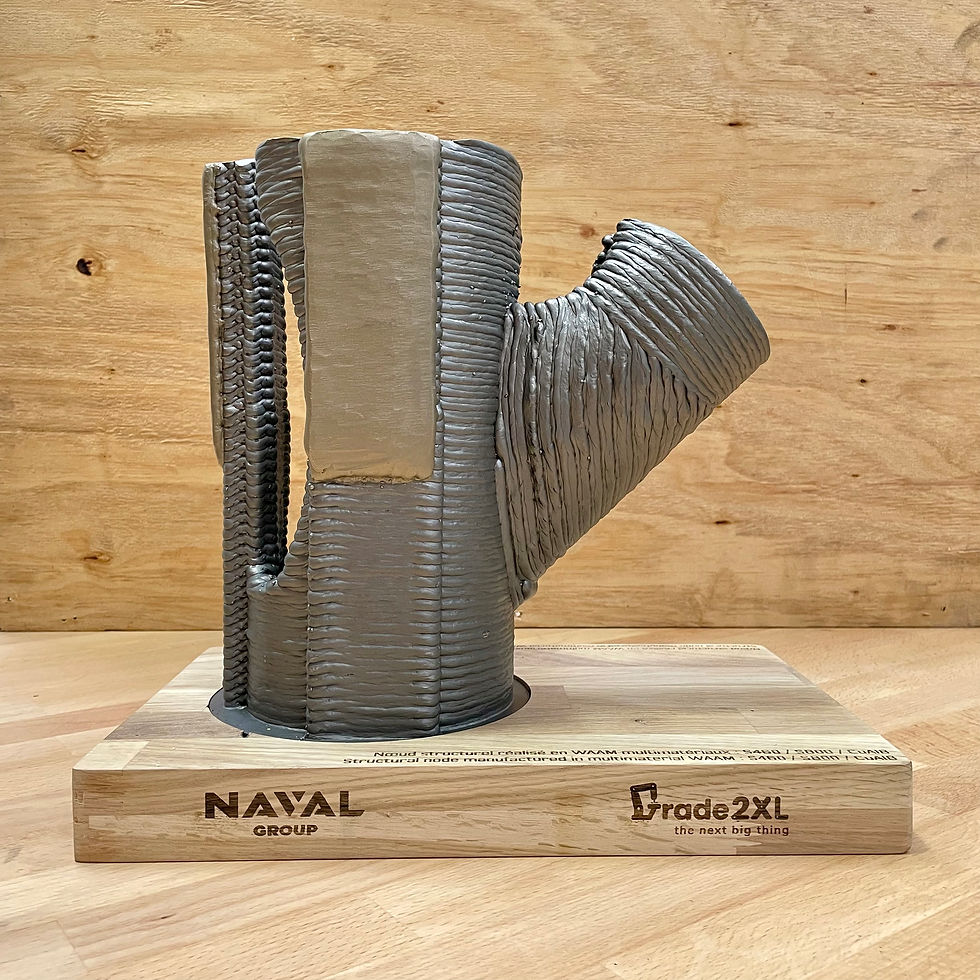
What is WAAM ?
This process of additive manufacturing leans on the welding process MIG-MAG with metal feeding shaped by wires. It is particularly adapted to manufacture metallic parts of great dimension and/or complex geometry. “The welding robot enables to generate the deposition trajectory requested. This technology allows freedom for the size and the design of the parts. It requires less raw materials than a classical process” explains Anne-Sophie THORR who is welding engineer at Naval Group.

Enough to seduce many industrials ! And that’s not all of it: WAAM offers other advantages. The deposition rate is high which allows to sharply reduce the production time, the initial investment for the machine is relatively cheap. In addition, the raw materials (coming as welding wires) are varied. Indeed, many metallic alloys are available. They are well-mastered and easily supplied.
The challenge: multi-material WAAM
Industrials already produce mono-material parts with WAAM. It had been demonstrated and used with many metallic alloys. However, multi-material WAAM is to be developed. Grade2XL aims at changing the metal used when manufacturing a part so it becomes possible to locally give specific mechanical properties to the part such as anticorrosion. Less noble material (so less expensive) would be used for the rest of the part. “It allows us to create parts which are more functional and reduce production costs” acknowledges Anne-Sophie THORR. In 2020, Grade2XL launched a yearly design contest to promote multi-material WAAM. This contest is open to students, young engineers in companies and researchers. It challenged the emerging community of practice to design an innovative product. The product should be multi-material and must be manufactured using WAAM technology. Naval Group is a member of the jury that choses the finalists of the Design Contest. Then, the company had produced one of the two winning parts: the one designed by Jan REIMANN, student at the Technical University Ilmenau (Germany). Read the dedicated article of Grade2XL Website.

It had been manufactured at the end of May 2021 with the WAAM robotic cell of Naval Group belonging to the Direction Technique et Innovation de Nantes-Indret located in the West of France. The part is a node structure with multi-material structure, with an anti-corrosion layer. I.e. it joins two structural parts. It used topology optimization to adequately distribute the matter to efficiently ensure the mechanical performances which is innovative.
Demonstrators to skill up
In addition to manufacturing this part winning the Grade2XL Design Contest, Naval Group will also produce two demonstrators for the project. A mobile ring for EDF (French energy supplier) and an injection mold of plastic parts for ARRK (industrial tool manufacturer, among others). These large parts (more than a meter long) feature specific characteristics such as cooling canals embedded in the injection mold. ”Producing the demonstrators enables Naval Group to increase its technical skills for manufacturing and controlling the quality of large parts as well as functionalizing it. In other words, the capacity to change material for specific areas of the part according to the properties expected (anti-corrosion, anti-fretting, anti-abrasion, etc)” says Anne-Sophie THORR. Consequently, for Naval Group, multi-material WAAM opens up to new possibilities whether new construction or maintenance.
Comments